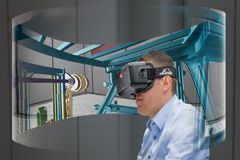
14/12/2015
Il Linde Safety Pilot del costruttore tedesco monitora senza sosta i parametri principali del carrello, come l’altezza di sollevamento, il baricentro e il peso del carico, l’inclinazione del montante, l’angolo e la velocità di sterzata, e avvisa l’operatore ogniqualvolta il carrello inizia a operare in aree critiche. Su richiesta il sistema LSP interviene attivamente nel controllo del carrello, ad esempio diminuendone la velocità o limitando il movimento del montante. In tal modo Linde ha reso attuabili miglioramenti significativi nell’ambito della sicurezza nell’utilizzo dei carrelli elevatori.
Verifiche virtuali con la soluzione “Hardware in the Loop"
Parallelamente allo sviluppo dell’LSP, gli ingegneri Linde hanno impostato la cosiddetta procedura di verifica “Hardware in the Loop" (HIL) che permette di esaminare, su modelli virtuali di carrelli, sistemi complessi come l’LSP e altre unità o sistemi di controllo elettronico e di svilupparli ulteriormente sulla base di queste analisi. Il Linde Safety Pilot è stato reso disponibile prima di tutto per i carrelli elevatori elettrici con portata da 2 a 5 t. Linde Material Handling offre 34 diversi modelli in queste due serie, oltre a diverse varianti di montante e attrezzature per la presa del carico – il sistema di assistenza deve essere configurato e testato per ciascuna di queste varianti. “Realizzare prove sul campo del sistema LSP per ogni singola variante di carrello disponibile non solo comporterebbe costi elevati, ma risulterebbe anche troppo dispendioso in termini di tempo - spiega Hans-Joachim Wenzel, che può volgere lo sguardo indietro ai suoi 27 anni di esperienza nel reparto di sviluppo e progettazione tecnica Linde, e che dal 2003 dirige il reparto di collaudo carrelli presso il centro R&D di Linde Material Handling - Con la nostra procedura “Hardware in the Loop", i collaudi possono essere realizzati molto più velocemente e a costi ridotti. Inoltre, possiamo testare nuovi e avanzati sviluppi sul modello virtuale di carrello e introdurre molto più velocemente di prima innovazioni nella produzione su scala industriale".
Ecco cosa è cambiato nelle tecniche di collaudo
Gli ingegneri di collaudo devono verificare che tutti i sistemi elettronici, e in particolare i sistemi relativi alla sicurezza, compresi i sistemi elettronici di sterzatura, il controllo del montante tramite joystick ed i complessi sistemi di assistenza come il Linde Safety Pilot, garantiscano affidabilità di funzionamento in tutte le condizioni ambientali. In caso di guasto, i sistemi integrati di monitoraggio e sicurezza devono riportare il carrello a una condizione sicura.
In passato, per realizzare i test necessari, il carrello e le unità di controllo venivano collegati ad adattatori di misura e venivano sottoposti manualmente a corto-circuiti, interruzioni e segnali di interferenza. Ciò serviva a verificare che, per esempio, tutte le operazioni di accensione, ridondanti per motivi di sicurezza, non permettessero un movimento non intenzionale del carrello. Ad ogni modo, tale procedura richiedeva l’esecuzione di diverse migliaia di singole fasi di prova, da valutare e documentare.
Pertanto Linde ha introdotto un sistema parzialmente automatizzato per il collaudo dei sistemi elettronici sui carrelli reali, come avveniva precedentemente. Oggi questa procedura detta “Vehicle in the Loop" sta venendo gradualmente rimpiazzata dal sistema HIL. I modelli di software generati a computer si basano sugli innumerevoli dati provenienti dal sistema CAD, così come dalle misurazioni e dai test, e forniscono una mappa virtuale del carrello elevatore con tutte le sue caratteristiche di guida. Ciascun modello calcolato viene poi adattato ai corrispondenti dati misurati sul carrello di riferimento reale finché la simulazione ed i test reali non forniscono gli stessi risultati. In tal modo, si viene a creare un kit di modelli che copre tutti i tipi e tutte le varianti delle funzioni opzionali ed in base al quale gli ingegneri configurano i carrelli di prova nel sistema HIL. Così l’impatto dei nuovi sviluppi sulle caratteristiche di guida può essere valutato senza dover costruire e testare dei prototipi, con un approccio assolutamente efficiente in termini di tempo e di denaro.
Vista virtuale a 360 gradi dal carrello elevatore
Nel reparto collaudo carrelli di Linde Material Handling vengono introdotti metodi di test basati su software. Tali metodi vengono utilizzati anche per i collaudi standard che permettono di verificare l’affidabilità di funzionamento dei carrelli elevatori. Insieme all’azienda di software Renow, Linde ha sviluppato un sistema IT per l’analisi del campo visivo in conformità alla normativa ISO 13564. All’interno di questo sistema viene generata una vista 3D del veicolo, basata su dati CAD, e un ingegnere di sviluppo, che indossa appositi occhiali, può valutare la visibilità dalla posizione dell’operatore con una visione a 360°. Così le prove del campo visivo possono essere realizzate nel rispetto delle norme già all’inizio della fase di sviluppo e montanti di sollevamento di nuova concezione possono essere collaudati e migliorati allo scopo di garantire una visibilità ottimale attraverso gli stessi.
Un team di ingeneri ed esperti collaudatori al servizio della sicurezza
I nuovi metodi di test basati sull’IT costituiscono soltanto una parte del programma di collaudo globale in cui Linde Material Handling verifica che i carrelli rispettino le normative inerenti ai requisiti di sicurezza, oltre a soddisfare le restrittive esigenze autoimposte dall’azienda in merito a sicurezza, durata e prestazioni anche in condizioni di funzionamento gravose.
A questo scopo, Linde ha sviluppato una serie di metodi di collaudo specifici e nel corso degli ultimi anni ha realizzato un centro collaudo con sei piste di prova e un corso di guida, 25 ampi banchi di prova per il collaudo dei componenti, così come una varietà di altri piccoli banchi. Vi lavorano 110 ingegneri, tecnici e collaudatori che durante i mesi del collaudo di resistenza testano componenti e sotto-assiemi. Inoltre, controllano la stabilità al ribaltamento dei carrelli e la loro adeguatezza per un utilizzo a temperature estreme, oltre a misurare e valutare l’impatto degli incidenti sul carrello e sulla sicurezza dell’operatore. In questo ambito viene anche eseguita una serie di crash test e prove d’urto. Carichi ed oggetti vengono lanciati sul carrello e alcuni componenti come gli sportelli del vano batteria vengono fatti sbattere contro le forche del carrello elevatore per assicurarsi che la batteria non venga danneggiata e che sia l’operatore sia l’ambiente rimangano in condizioni di sicurezza.
Share :