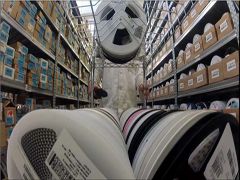
Il Gruppo Elemaster è una realtà di rilievo mondiale nel campo della produzione elettronica, dal circuito stampato, fino all’assemblaggio e alla produzione di schede e sistemi elettronici completi. Nello stabilimento produttivo di Lomagna (Lecco), dove avviene l’approvvigionamento dei componenti elettronici, di dimensioni microscopiche (e di altri componenti e materiali di dimensioni eterogenee), incontriamo l’architetto Luca Ceppi, managing director di Elemaster che ci racconta l’innovazione introdotta. “La logistica di produzione è molto diversa dalla logistica del prodotto finito - spiega Ceppi - Si può definire come un grande kanban a servizio della produzione“. Si è partiti, quindi, dalla consapevolezza, nata a livello manageriale, che un’azienda caratterizzata da processi produttivi altamente complessi necessita di sistemi che gestiscano le operazioni ottimizzandole e minimizzando sprechi ed errori. Tale consapevolezza si è tradotta nella decisione di adottare un sistema in grado di portare maggiore sicurezza ed efficienza nella gestione dei materiali. Per svolgere questo progetto Elemaster ha scelto Kube Sistemi, che con oltre duecento progetti all’attivo nella logistica, ha customizzato il WMS proprietario Gulliver in base alle esigenze espresse dall’azienda con l’obiettivo di ottimizzare i processi logistici legati alla produzione.
I benefici ottenuti
Una gestione più efficiente dei materiali: il sistema Gulliver dispone di algoritmi che
consentono di scegliere in automatico i punti di prelievo dei materiali
indirizzando l’operatore a colpo sicuro. Ciò genera l’ottimizzazione dei
materiali utilizzati e un risparmio di tempo sull’intero processo, anche in
relazione al lavoro degli operatori.
Miglioramento della tracciabilità: grazie all’inserimento del numero di lotto fin dal ricevimento e alla gestione di questa informazione in automatico lungo tutto il percorso dei materiali e dei prodotti, è possibile in ogni momento rintracciare le informazioni sui materiali e sull’avanzamento del processo.
Eliminazione dell’inventario: le informazioni di inventario si ottengono dinamicamente e in tempo reale ad ogni singola movimentazione di materiali. Ciò ha reso superfluo l’inventario di tipo tradizionale, effettuato periodicamente e con fermo attività.
Risparmio delle risorse necessarie per le attività del magazzino: il sistema è in grado di effettuare lo stesso numero di prelievi (circa 12mila codici a settimana), innanzitutto senza errori, e poi con meno fatica e con meno persone che possono essere destinate allo svolgimento di altre funzioni, in magazzino o altrove.
Drastica diminuzione dei fermi macchina: i fermi macchina, dovuti ad errori di prelievo (che possono costare anche migliaia di euro) sono drasticamente diminuiti, con un vantaggio incalcolabile sull’efficienza della produzione.